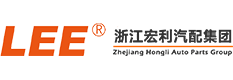
●This is Honglee
Zhejiang Honglee Auto Parts Group, headquartered in Pinghu, Jiaxing, Zhejiang, known as the "Golden Pinghu", was formerly known as Zhejiang Yuhuan Wanxiang Drive Shaft Factory, founded in 1987. After more than 30 years of steady development and accumulation, the company has grown into a professional and specialized high-end manufacturing group enterprise focusing on automotive chassis parts. The group currently has three production bases, located in Pinghu, Jiaxing, Huzhou Changxing and Thailand, and has more than 10 subsidiaries including Zhejiang Kangpurui Auto Parts Co., Ltd. , Zhejiang Defu Precision Drive Manufacturing Co., Ltd., Zhejiang Honglee Auto Parts Co., Ltd.
The transmission shaft standard parts of Kangpurui, a subsidiary of the group, have achieved a cumulative sales volume of more than 200 million units/year with sales volume of more than 40 million units. The shock absorber top rubber of Hongli Automobile covers more than 80% of the US market models, and the transmission shaft dust cover has achieved annual sales of more than 10 million units, covering almost all models in the world. The products of the group are supported by well-known domestic and foreign manufacturers such as SAIC, Honda, Nexteer, ContiTech, NTN, etc., and are applied to various car series such as Mercedes-Benz, BMW, Audi, and Honda. They have been fully recognized by customers and have won honors such as "Quality Excellence Award", "Service Excellence Award", "Strategic Cooperation Award", and "Cost Excellence Supplier" from customers.
1987year
Founded in
10More than
Subsidiary
88Million more than
Annual production of products
133708㎡
Covered area
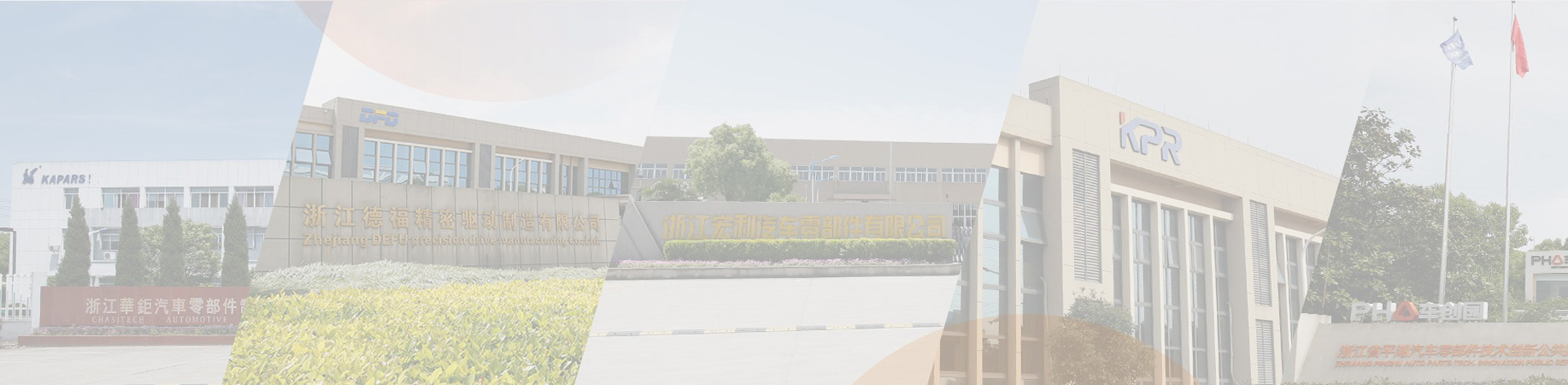
Subsidiary companies of the Group
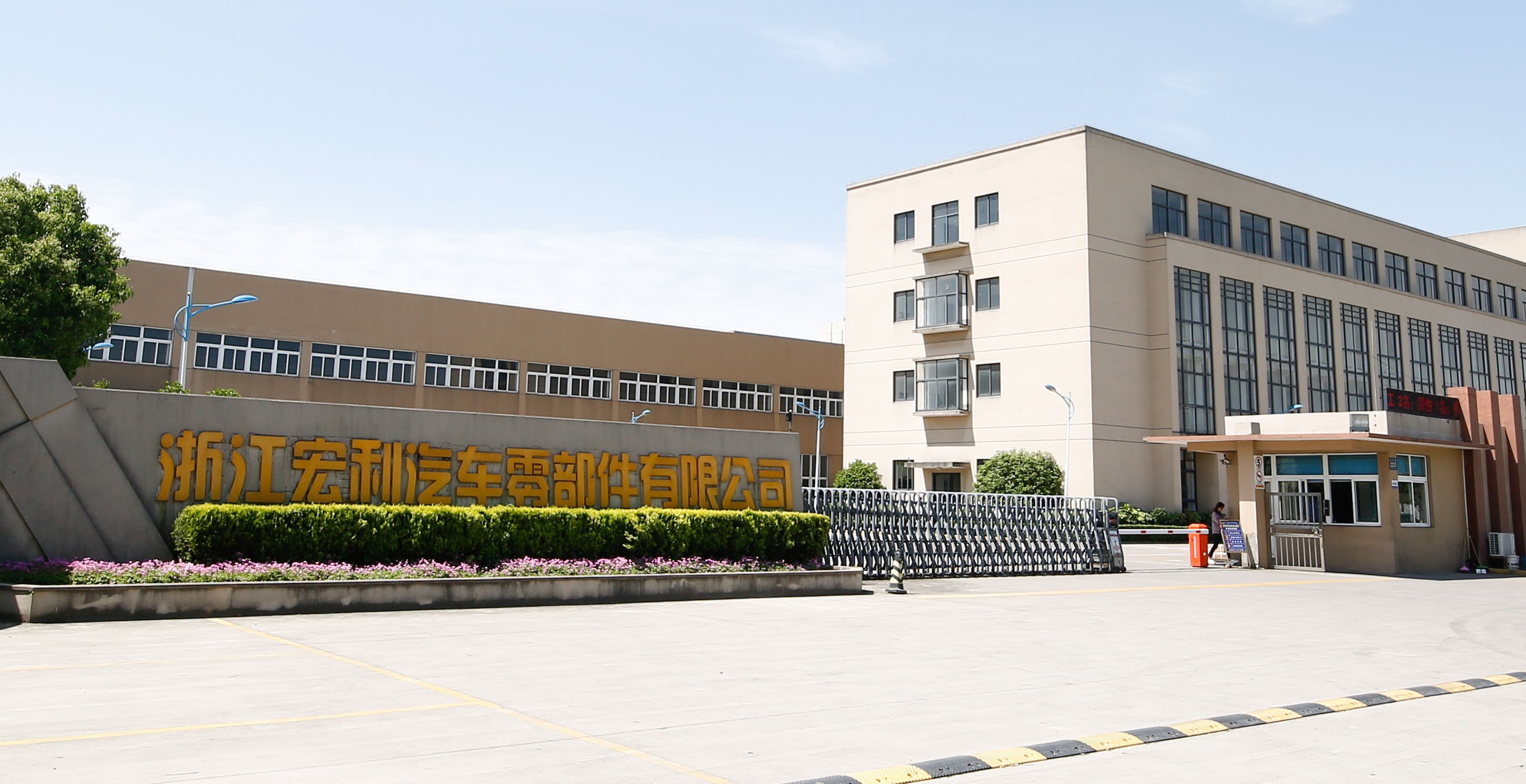
Hongli
Zhejiang Hongli Auto Parts Co., Ltd.is located in the Jiaxing Pinghu Economic Development Zone, and is a professional manufacturer of automotive chassis rubber shock absorbers.
Our main products are: constant velocity universal joint ball cage dustproof sleeve, shock absorber isolation block assembly, engine support and other chassis rubber shock absorbers.
Hongli has introduced German DESMA vulcanization production lines, German OSSBERGER (Oxenburgh) blow molding automatic production lines, and introduced a mixing center. Automation has improved the manufacturing process to be more controllable and stable. The company uses an ERP information management system, implements computerized management for production, supply, and sales, and has established its own office automation system. Barcode management and the first-in, first-out principle are implemented for material and product flow, improving production efficiency. The company has passed IATF16949, ISO14001 and other system certifications, and runs comprehensively. In terms of quality testing, the company has material testing equipment such as Mooney viscosity, vulcanization characteristics, rubber strength, and rubber weather resistance testing equipment, as well as finished product testing equipment such as three-coordinate size measurement, rubber creep, elastomer dynamic testing equipment, high and low temperature endurance testing equipment to effectively monitor and control the manufacturing process.
In terms of research and development, the company has two-dimensional/three-dimensional design software such as CAXA, Catia, ABAQUS and other software design platforms, as well as PLM research and development management systems. At the same time, it has obtained 9 national invention patents and 54 utility model patents. The company has developed hundreds of products for mainstream car models of German Mercedes-Benz, BMW, Audi, Volkswagen; American Buick, Ford; Japanese Toyota, Honda, Nissan, Mazda, etc., with rich experience in product development. The company has cooperated with universities such as Northwestern Rubber Institute and Jiaxing University to continuously improve its research and development design capabilities to meet the synchronized development strategic needs of various automotive manufacturers.
The company has always been committed to the business philosophy of "honesty, cooperation, and efficiency", upholding the marketing philosophy of "making good products and providing customers with value for money", and cooperating with various parties for win-win results to bring true manufacturing advantages to consumers.

Kangpurui
Zhejiang Kangpurui Auto Parts Co., Ltd. is located in Pinghu City, Zhejiang Province, a national economic development zone. It is within the 100-kilometer economic circle of Shanghai-Hangzhou-Ningbo, and is the first stop from Shanghai to Zhejiang.
The company's main business is the production and sales of automotive transmission shaft standard parts. It has production equipment such as German Epson heat treatment equipment, Japanese OKUMA fully automatic processing line, Japanese NACHI broaching machine, Japanese MURATEC double spindle lathe, German GEORG six-window punching machine, Taiwan Jinfeng punching machine, Ningxia Little Giant CNC, and Tsugami Precision's three-pin shaft professional machine tool. At the same time, it has testing equipment such as spectrometer, Measuring instrument, roughness profile meter, roundness tester, projector, universal industrial microscope, etc.
At present, the annual production capacity has reached 7 million three-pin shafts, 10 million inner star wheels, and 20 million cages (ball cages). The products are mainly supplied to Shanghai Natick for supporting Shanghai Volkswagen, Shanghai General Motors, FAW-Volkswagen, Mercedes-Benz, BMW, Changan Ford, and Shenlong Fukang, etc. The goal is to become China's largest manufacturer of standard parts for transmission systems, and the cage is currently one of the largest production enterprises in China.
With the continuous development of the company, the company's production equipment, testing equipment and other hardware have been continuously upgraded, which has further promoted the automation transformation and upgrading of the company while expanding production capacity, ensuring the stability of product quality. Relying on technological accumulation and continuous independent innovation, the company takes "zero defect" as its direction of endeavor, continuously provides competitive products and services, and gradually grows into an excellent provider of standard parts for automotive chassis driveshafts.
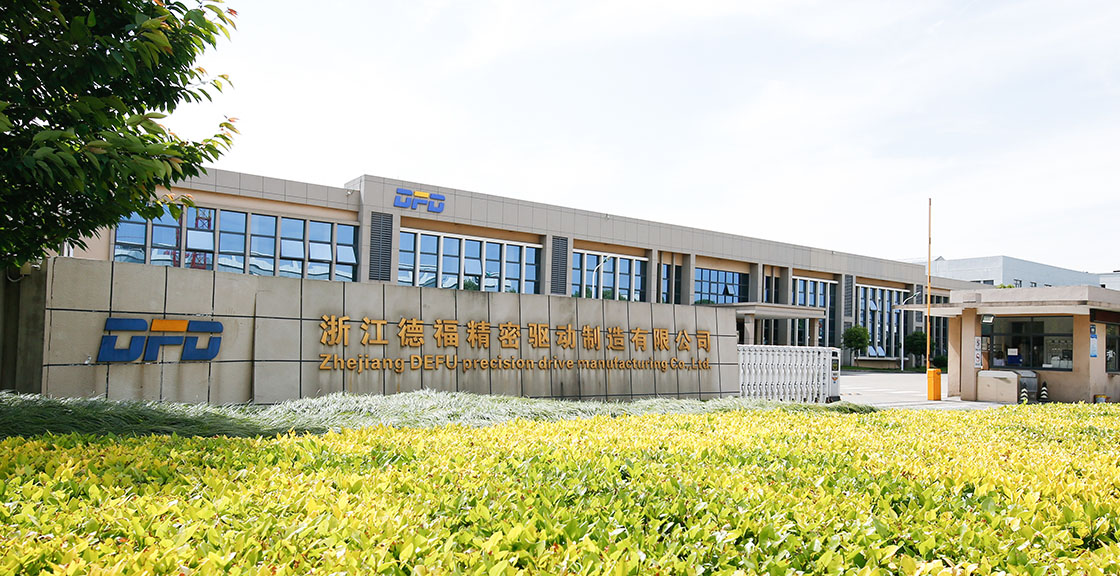
Defu
Zhejiang Defu Precision Drive Manufacturing Co., Ltd. is located in Pinghu, a beautiful water town in the south of China.
As a leading enterprise in the industry focusing on the manufacturing of shaft forks, intermediate shafts, and electric drive connecting shafts for transmission shafts, Zhejiang Defu Precision Drive Manufacturing Co., Ltd., founded in 2014, focuses on talent cultivation, maintains perennial cooperation with universities, and has a group of knowledgeable R&D technical teams.
The company also continues to invest in building advanced and intelligent manufacturing lines, using internationally renowned machining production equipment; adhering to quality priority and excellent cost control as the guide, applying advanced management systems to ensure satisfactory products and services for customers.
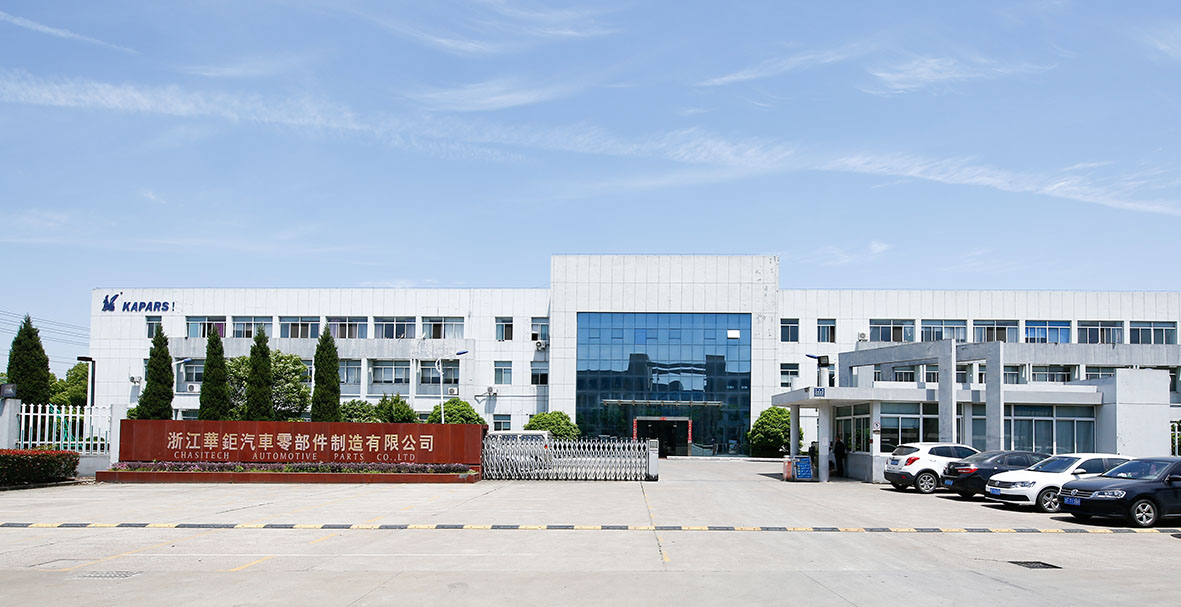
Huaju
Zhejiang Huaju Auto Parts Manufacturing Co., Ltd. was established in September 2006. It is mainly engaged in the research and development, production, sales and maintenance of automotive parts. The products are mainly sold domestically and are currently expanding their export business.
Our company produces nearly 1,000 different types of outer ball cages, with an annual production of over 1.5 million sets. The main car brands include American (GM, Ford, Chrysler), European (Volkswagen, Citroen, Peugeot, Fiat, Renault, Opel, Volvo, Alfa Romeo, Land Rover, etc.), Japanese (Toyota, Nissan, Honda, Mitsubishi, Mazda, Fuji, Daihatsu, Suzuki, Isuzu, etc.), Korean (Hyundai, Daewoo, Kia, SsangYong, etc.), domestic (Geely, Chery, etc.), as well as various microcars and passenger cars.
The company has 120 sets of professional production equipment and nearly 150 employees, including more than 20 senior professional and technical personnel and numerous skilled operators of CNC machine tools. The annual production capacity is over 1.5 million sets. It is exported to more than ten countries and regions such as Southeast Asia, Russia, Europe, America, and Africa, and is trusted by users. Zhejiang Huaju Auto Parts Manufacturing Co., Ltd. is a professional manufacturing enterprise specializing in the production of automotive transmission systems - outer ball cage.
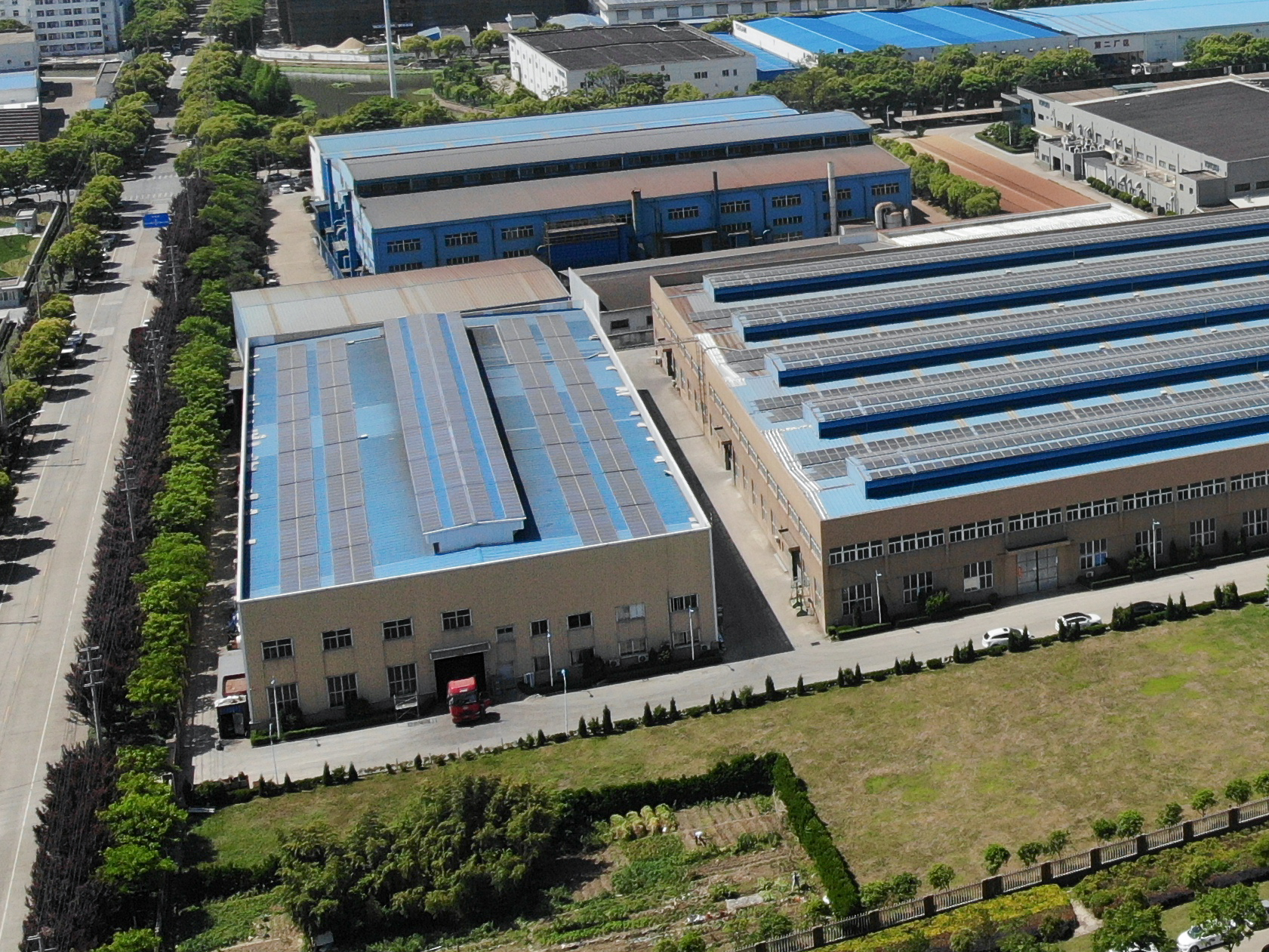
Kejin
Jiaxing Kejin Machinery Manufacturing Co., Ltd. was established in April 2014. It is a company specializing in the production of ball cage type constant velocity joints and hot forged and warm forged inner and outer ball cage blanks.
The company is located in Pinghu, Zhejiang, which is the supporting base for China's automobile assembly plants. After more than 9 years of efforts and development, the company has achieved a certain scale and strength. It now has a skilled forging team with a monthly forging capacity of over 400,000 pieces. With the demand for automotive parts in China, a one-stop production of blanks and finished products has been formed in 2016, which has enabled the company to achieve unprecedented development. In October of the same year, it passed the ISO9001-2000 version of the product quality system certification.
The company adheres to the business philosophy of customer first and service first. Respecting talents and focusing on technology, it always pursues product quality both internally and externally, and strives to provide more customers with products that are like handicrafts.
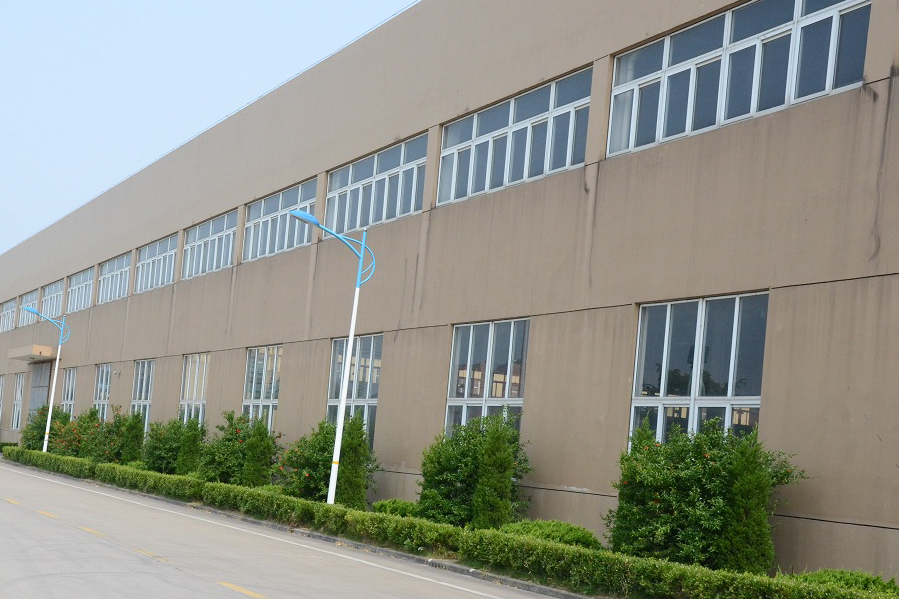
Yipu
Zhejiang Yipu Network Technology Co., Ltd. (referred to as Epu Company) is committed to building the EEP brand - China's most outstanding chassis component integration service provider, and has been committed to developing into an expert in automotive chassis components in the domestic market.
Yipu Company is supervised by the quality system of the Japanese company Tohoku Industry, and is jointly provided with technical guidance by Pinghu Automobile Parts Inspection and Testing Center, Zhejiang University and Tongji University. At the same time, it has strategic cooperation with supporting factories such as SAIC Group, FAW Group, Dongfeng Honda, Guangzhou Honda, Geely Automobile, Chery Automobile, etc. It is located in the Japanese Industrial Park in Pinghu, Zhejiang Province, which is a national economic development zone. It is adjacent to Shanghai in the east and Hangzhou in the west, with unique geographical location, convenient logistics and national radiation.
EEP focuses on improving product quality and developing new products. We strictly follow the TS16949 automotive quality system process from design, development, and manufacturing, and introduce German Cai's three-dimensional coordinate, Maer precision measurement equipment, and Japanese Mitutoyo precision instruments to control quality. At the same time, we develop and produce high-quality products for different regions, climates, and road conditions. Currently, EEP has its own brand "EEP", and its product series includes: ball cage, shock absorber, swing arm, ball head, top rubber and other chassis parts, covering all passenger car series in the Chinese market, with about 10,000 models.
Quality first, adhere to the production of the safest chassis components, have the most complete product models, and strive to build the EEP brand - China's best chassis component integration service provider.
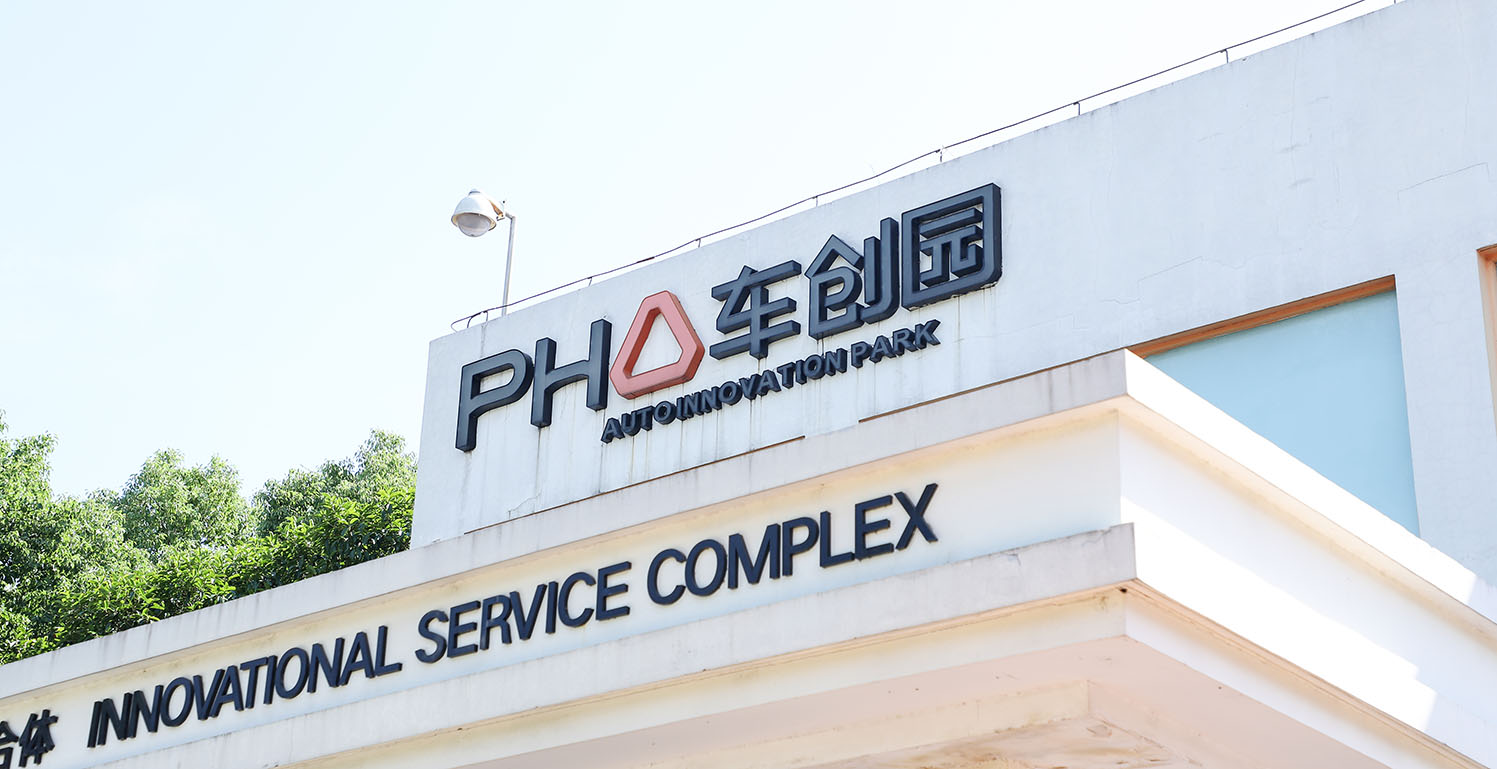
Chechuangyuan
Pinghu Chechuangyuan is a comprehensive platform for automotive parts jointly created by an automotive parts industry investment company and a professional incubator management team. In 2019, it was awarded the Jiaxing Municipal Professional Incubator and the list of Zhejiang Province's automotive parts industry innovation service complex.
The incubation platform of Pinghu Chechuangyuan focuses on the growth needs of auto parts enterprises, gathers various factors and resources, and provides services such as entrepreneurial space, inspection and testing, technological innovation, scientific and technological consulting, investment and financing, entrepreneurial incubation, etc. for Pinghu and the Yangtze River Delta auto parts enterprises and project innovation and entrepreneurship. It adopts an incubator management + investment and financing management + market development + industry integration + entrepreneurial counseling and support + technological innovation service + production, learning, research and application as one of the incubation modes, and high-tech, high-growth, high-value-added projects grow rapidly and form industrialization channels.
The Pinghu Automotive Parts Industry Innovation Service Complex in Zhejiang Province adheres to the principle of government guidance, enterprise participation, and the joint participation of universities, research institutes, industry associations, and professional institutions. It focuses on cultivating new driving forces and repairing traditional driving forces, gathers various innovation resources, and deploys functional sectors such as industrial technology innovation system, government-industry-university-research-application collaborative innovation system, innovation and entrepreneurship service system, and innovative public service system based on the current situation and development trend of industrial development, so as to continuously optimize the regional industrial development ecology.